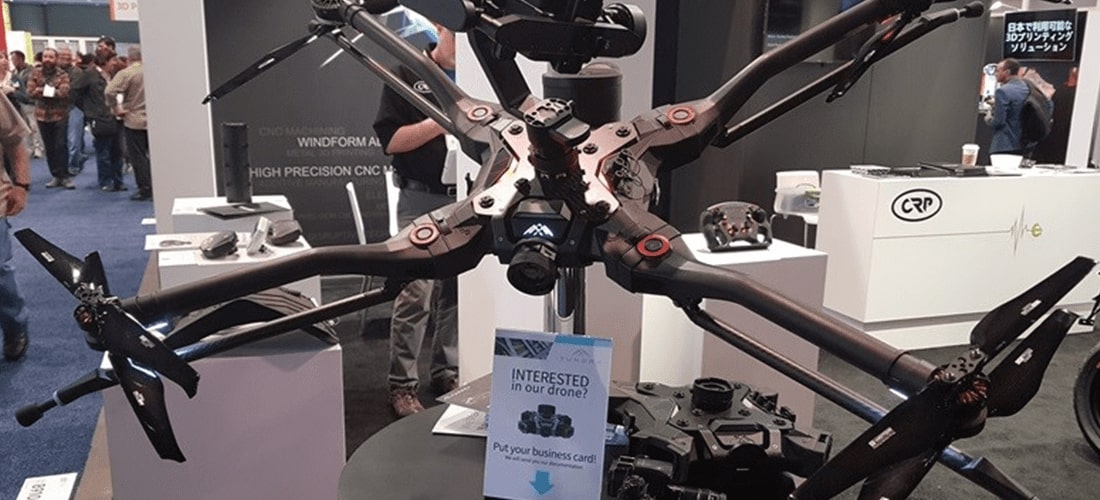
Drones were first developed in a military context but are now playing an increasingly important role in civil contexts too. And recently their use in the nautical world has stepped up considerably.
Drones are used for leisure and for rescue. And small, easy to use underwater drones are used for hull-cleaning and are encouraging environmentally-friendly anti-fouling procedures.
Rescue drones already used by the United States Coast Guard service will soon be available on the civil market. These small remote-controlled boats can quickly carry a self-inflatable craft to shipwrecked persons in any weather conditions.
The Tundra-M, a professional modular drone built using Windform® and 3D printing looks especially interesting, in view of its numerous uses in the nautical sphere, its modular design and the materials used to make it.
Perfect for nautical use
Tundra-M is a modular working prototype produced using selective laser sintering (SLS) technology and Windform® composite materials. Developed by CRP Technology for the motorsport industry, these composites are now being used in a wide range of applications in the most advanced sectors: like the nautical world, for example.
The Tundra-M project involved CRP Technology and Hexadrone, a French company that is leading the field in the construction of industrial and multi-functional drones.CRP created the Tundra-M prototype using professional 3D printing and two carbon fibre-reinforced composite materials. The four arms are made of Windform® XT 2.0, while the main structure (central body/fuselage/bodywork) is made of Windform® SP.
A modular drone
The drone was designed by Hexadrone and from the outset the idea was to use composites to create the various components. The focus of the project was to create a “modular” drone: a drone that can be assembled and dismantled. The Tundra-M consists of a two-part frame, joints, a system (patented by CRP) to rapidly attach and detach the parts, and components forming the mobile arm system (patented by Hexadrone).
This technology and these materials have generated notable savings in time and money. A rapid iteration process was needed, as well as the best possible relationship between structural resistance and weight and the production of a multi-function prototype.
All of these specifications were satisfied in full using laser sintering technology and Windform® composite materials. This makes it possible to produce working prototypes that enjoy all the advantages of injection moulding, but without the disadvantages of this traditional technology in terms of costs and timescales.
The materials selected for the prototype have similar properties and features -- such as density, colour, breaking load, modulus of elasticity, modulus of resistance and elongation at rupture -- to the materials that will be used during production. So it was possible to test the prototype in real conditions.
The central body and the supporting feet are made of Windform. The body, which consists of the frame and a removable cover, contains the Tundra-M’s nerve centre: the main circuits and the cooling system.
A strong, resistant and waterproof material was needed for the body: not only is it equipped with a two-battery emergency parachute, but it is the structure to which the four extractable modular arms are attached. For this reason, a carbon fibre-reinforced composite material was chosen.
The central body of Tundra-M
The removable supporting arms, which can be replaced using a locking and unlocking device, were also made from the same carbon fibre-reinforced composite.The arms, produced using professional 3D printing
The use of SLS technology combined with composite materials made it possible to considerably reduce costs with respect to plastic injection moulding. From an economic perspective, injection is viewed as too risky, especially if design flaws are noted after the mould is made. In addition, the thermal properties of the materials used in SLS are particularly well-suited to drone prototypes, as are their mechanical properties, making these materials very competitive.
The Tundra-M prototype was rigorously tested. Tests included the assembly/dismantling of the various parts to check the structure and the fatigue strength of the composites; landing tests, in which the feet of the drone must be able to bear the weight of the device and the stresses caused by the opening and folding of the landing systems; and flight tests, to determine whether the assembled parts can handle the stresses connected with the numerous flight scenarios. All of the tests fully demonstrated the high degree of reliability of these 3D-printed composites.
Tundra®, the first Hexadrone drone (completely modular and easy to use), was designed by Raphael Chèze and won the Red Dot Award 2018 for the drone category.
Selective laser sintering
SLS technology was invented by Carl Deckard at the University of Texas at Austin in 1984.
In the SLS process, microscopic plastic particles (nylon powder) are exposed to a high-power laser which fuses and moulds them to create a three-dimensional solid object.
The powder is first spread onto a platform to create a layer about 0.1 mm thick. The powder is then hit by the laser, which melts it into a compact layer. Any non-sintered powder on the platform acts as a base for the subsequent layers, and so on until the object is complete. At the end of the process the object is detached and any non-sintered powder is removed.
Selective laser sintering using carbon fibre-reinforced composite polyamide (nylon) material
Windform® SP, produced by CRP, is a carbon-reinforced polyamide-based material. It is deep black in colour. The material has high resilience and elongation at break values, as well as high thermal properties and resistance to high temperatures and to liquid and moisture absorption. These properties make it possible to produce accurate, reliable and long-lasting prototypes and are perfect for functional applications.
Windform® SP is recommended for all applications that require resistance to damage, vibration, deformation and high temperatures.
Share your stories on leisure marine industry with us
Do you have an innovation, research results or an other interesting topic you would like to share with the leisure marine equipment industry? The METSTRADE website and social media channels are a great platform to showcase your stories! Let us know via metstrade@rai.nl
Are you a METSTRADE exhibitor?
Make sure you add your latest press releases to your Company Profile in the Exhibitor Portal for free exposure.