Composite material breakthrought: truly sustainable and fully recyclable
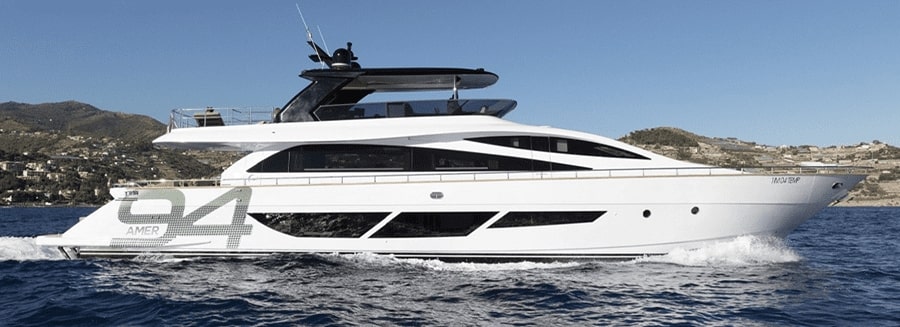
Since 2014, the subject of how to handle the increasing number of redundant boats, and in particular, the difficulties of recycling traditionally employed glassfiber (GRP) composites, has been on the agenda at METSTRADE.
A regular speaker and contributor at most of these forums has been Enrico Benco, an enthusiastic ecopreneur, who started his company Go Sailing For a Change (GS4C), with the objective of developing a new fully recyclable composite material for yacht construction.
Enrico recognised that one of the key challenges to recycling GRP, is that separating the glass strands from the resin with any degree of success, whilst retaining original material integrity, and minimising energy consumption in the process, has been proven to be a very elusive proposition.
Since 2012 he has worked with various partners in an adventurous project to incorporate an enriched basalt (volcanic) fiber into a construction material matrix. By combining with a bio-based epoxy resin, the resulting composite can go back into a low-energy furnace at end-of-life to be reconstituted to its original state, and used again in yacht construction.
Step by step progress
Along the way, Enrico and his collaborators, including his partner Christiana Talon have worked hard and registered some successes. At the World Sailing annual conference in 2017 where the Sustainability 2030 initiative was launched, his plans to build a sustainable ‘cradle to cradle’ Mini Transat sailing boat called the Loop650, were enthusiastically received. And as we reported last year, the Loop650 project utilising enriched basalt / epoxy resin composite, was nominated for the JEC Innovation Award in the Sustainability Category.To briefly recap, the JEC Group are the largest composites organisation in the world, and the main benefits of the material were acknowledged by their awards committee to be as follows:
* Industry / boatyard ready.
* Cradle to cradle recycling. (Reuse for new boats at end-of-life)
* Zero landfill at end-of-life
* Low embodied energy
* Circular economy for boat building / industrial composites.
Note: The material, called FILAVA® is softer and easier to handle than Fiberglass, yet offering aerospace and ballistic grade mechanical properties. It also has higher fire resistance characteristics.
Amer Yachts, first superyacht builder to take the leap!
Barbara Amerio is the second-generation owner of Amer Yachts, part of the Permare Group, established back in the 70’s by her father Fernando. She has spent more than 30 years working in the family business specialising in superyacht building, brokerage and refits, and she prides herself on driving the sustainability and innovation aspects of the yard’s production.
As a board member of UCINA, the Italian Marine Trade Organisation, Barbara was introduced to Enrico and Christiana of GS4C, and was immediately impressed with their knowledge of the sailing world, and their progress towards producing a truly sustainable, fully recyclable composite material.
Having signed a cooperation agreement with GS4C, and agreeing to adopt the FILAVA® material for future new builds, we asked Barbara to explain a little more about her decision.
“We would like to be a good example in the nautical sector for the next generations,” she said. “For example, being a strategic partner with Volvo Penta we have reached the best performances with our Amer 94 (28.65 m LOA) Here we have achieved 3,1 litres per mile consumption at 9 knots, powered by 2 x 1000 hp IPS 1350 hp engines.”
“I have studied for some time the objectives of the Circular Economy, and I’m very interested in improving the whole process for the end-of-life in yachting, it’s a problem which has to be faced sooner rather than later in our industry.”
“When I was introduced to the FILAVA® composite material, I immediately understood that we could introduce an epic change, by using this enriched basalt matrix, for not only the hull and superstructure mouldings but even the moulds. A cradle to cradle system will definitely solve the end-of-life problems that our industry has encountered for decades now.”
“So, we have started the first part of analysis and tests by RINA and Enea and have decided to choose a non-structural component to make from the new material, with a special team created in order to ultimately construct a future yacht entirely from this recyclable composite.”
Barbara admits that Amer Yachts are at the beginning of this adventure into innovation and improved sustainability. There are few small boats made in basalt, but she aims to be the first in the superyacht sector, and is sure that it will show a positive signal to others, as the yard have done by being the first to adopt the Volvo Penta IPS propulsion packages.
You can hear more from Barbara about her project, when she joins the ‘How Green are We” Sustainability Panel Discussion at METSTRADE 2019, on Wednesday 20th November at the I-nnovationLab Stage, at 13.15. Enrico Benco from GS4C is also planning to be there, to answer questions about the basalt composite material.
Share your stories on leisure marine industry with us
Do you have an innovation, research results or an other interesting topic you would like to share with the leisure marine equipment industry? The METSTRADE website and social media channels are a great platform to showcase your stories! Let us know via metstrade@rai.nl
Are you a METSTRADE exhibitor?
Make sure you add your latest press releases to your Company Profile in the Exhibitor Portal for free exposure.