Bio-based and recyclable materials prove themselves
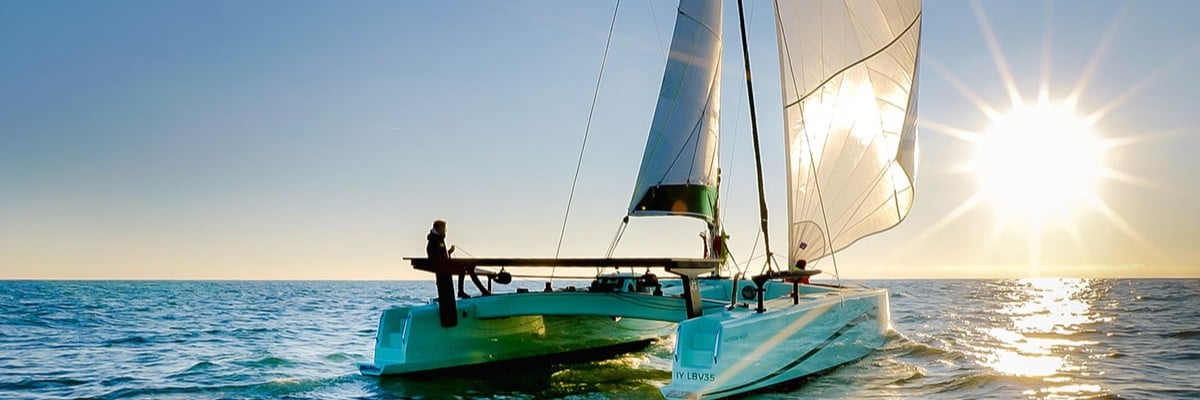
Life Cycle Assessment tool should demonstrate the advantage
Fibres from flax or volcanic rock, resins from lime seed oil or pine trees. Nature can provide the core materials for boat building composites to replace the synthetic materials that have been widely used over the last 70 years. Niche boat builders embrace the new and recyclable materials and prove durability. Bigger series production yards follow step by step, rationalising the new eco components for market readiness and cost efficiency.
Composites consist of fibres and resin bonded together to form a tough layer. Yacht hulls often consist of solid layers of glass fibre and polyester, for performance yachts this may be two layers of fibre and resin composite around a lightweight core of foam, honeycomb shaped cardboard or lightweight wood like Balsa. Once cured, the resin cannot be separated from the fibres. End-of-life yachts become landfill. The fibres and resins are synthetic, based on refinery of fossil oil. Nature provides renewable alternatives. Advanced chemistry can produce resins from these renewable natural materials that will cure to provide the strength and durability needed in yachts when they cure. The novelty is that these resins can be molten after the yacht’s end of life. The resin and fibres can be separated and re-used for a next boat or other purposes.
Bio is better
Pioneers show the way. The FX28 daysailer has proven applicability of flax fibres and lime seed oil based resin since its launch in 2019. The LBV35 is built from fibres derived from volcanic rock and recyclable epoxy resin. This daysailer catamaran for the eco-aware charter company La Belle Verde on the Spanish island Ibiza won the Ocean Tribute Award at the Düsseldorf boat show January 2023 for being the first fully recyclable composite production boat. The Sunreef Eco 80 foot motor catamaran uses both flax fibres and volcanic fibres in different areas of the construction. The first years of experience, backed by extensive scientific studies into the properties of the fibres and resins, show comparable, if not better characteristics of the bio-based and recyclable composites compared to GRP or even glass-epoxy or carbon-epoxy structures.
Flax
“I love boats and I like sailboats to perform well. Light-handed, balanced and fast sailing is a joy.” Friedrich Deimann connected to the audience in his speech introducing flax fibres and bio-based resin as the raw material for composite boat building, at the METSTRADE materials pavilion back in 2018. “But I hate the materials used in modern boat building. The glass fibre makes my skin itch and small slivers penetrate my skin, causing irritated skin for days. Polyester resin causes poisonous fumes while epoxy resin causes allergic reactions. These materials are oil based synthetic products, unhealthy and unpleasant for yacht builders and by origin harmful for the earth’s ecology. That is why I initially dedicated to wooden boat building. Yet, as beautiful a material as wood is, wooden hulls lack a competitive edge for sailing boats in terms of weight . Wood requires ongoing maintenance. I wanted an alternative, a nice and beautiful material to work with and one that would enable the construction of strong, lightweight hulls for sailing yachts.” An overview of the lengthy road towards developing a quality resin from natural materials is what followed in Deimann’s speech. His development led to the founding of Greenboats in the German town of Bremen. The FX28 daysailer, built from flax fibre and lime seed oil based epoxy resin, is the proof of concept. While the company Greenboats is already active for more than 10 years, the introduction of recyclable and sustainable materials in the marine industry is only slowly progressing. Some of the larger yards that produce composite yachts in series, are nowadays experimenting with eco-material components.
Volcanic Fibre
Focussing on performance sailing yachts, Austria-born Norbert Sedlacek Koch experimented on applying fibres derived from volcanic rock as a strong core material for composites in 2012. Belgian company Isomatex produces these fibres for application in aeroplanes and wind turbine wings. Basat fibres bond with epoxy resin to form a construction stronger than steel. Together with his wife Marion, Koch founded Innovation Yachts in Les Sables-d’Olonne in France, where the first yacht built is the Imoca-style 60-foot racing yacht AAL – an abbreviation of Ant Arctic Lab. To prove the durability of the basalt fibre construction method, Koch intends to set a speed record by navigating solo, non-stop and unassisted on this yacht from France, across all five oceans, including the Arctic and Antarctic Oceans. Five attempts have failed, AAL returned to the yard during the fifth attempt this summer after damaging the canting keel west of Ireland in a storm.
Volcanic fibre composite construction was also applied on the award-winning LBV 35 catamaran, a boat designed to tour the coast of Ibiza with twelve guests, generate electricity for the electric engines and the sound system while sailing and be fully recyclable and leave no pollution over its lifetime. The 16-foot lightweight sailing boat Open 16 Fipofix was the first prototype of Innovation Yachts can be ordered, like the 3.3 metre long dinghy ‘Lava330’. The epoxy resin used by Innovation Yachts is bio-based bto epoxy, an epoxy without solvents, which is not provoking allergies.
Zero emission
Polish yard Sunreef Yachts in Gdańsk builds luxury motor- and sail catamarans. Their 80-foot (24 metres) long Sunreef Eco is the first ready-built yacht from their line of Eco catamarans, ranging from 50 foot (16 metres) up to 133 foot (43 metres). The yard engineered a way to integrate solar panel into the composite construction of the hulls. The eco concept is not only to use bio-based and recyclable materials, but also to reduce emissions down to zero. Hydro generators and solar panels provide electricity for hotel functions and motoring in and out of harbours, while sails provide propulsion on open waters.
Sails from a bottle
Chemists that developed resins that cure to create a strong bonding to fibres, yet separate from the fibres after they melt at the composite’s lifetime, are the enablers of the recyclable yacht building technology. This technology is also used in sails. Italian sailmaker One Sails applies recyclable resins and glues in their 4T Forte sails. Danish sailmaker Elvstrom uses plastics from recycles soda bottles to produce their eXRP EKKO sails. Ocean racer Pip Hare is using recyclable sails on to test (and prove) durability of the recyclable sails.
Partial eco
Large scale yards like Groupe Bénéteau in France apply the new bio-based and recyclable materials on a modest scale. The ‘sustainable boat of the future’ as CEO Gianguido Girotto describes it, is the new Jeanneau Sun Fast 30 OD. This cruiser-racer sailing yacht is built with the recyclable resin Elium that contains 18 per cent bio component. For other yachts, the yard is making non-structural parts containing up to 35 per cent biosourced material. Cost, availability, quality control and proven technology are understandable considerations for large yards to wait for the outcomes of the pioneers’ experiments.
Develop boating LCA
“Life Cycle Analysis needs to be developed for the boating industry,” editor-in-chief Aaron Porter of Professional Boatbuilder magazine argues. “As the yards and suppliers in the marine industry are ready and willing to develop more sustainable products, we should develop objective measures to determine if all of these initiatives will significantly reduce the ecological footprint of a yacht over its lifetime.” It is of course a good thing to have yachts that are not destined to become landfill after 35 years. But how does that compare to replacing the diesel inboard engine for electric propulsion? If the energy of heating an oven to recycle the composites is taken in account, how does that affect the overall footprint? New material initiatives show potential. At a first glance, the outcome in a LCA appears to be positive with the use of the new eco-aware materials. “Like other industries, yacht building will be subject to regulations that demand a proper LCA for any yacht produced,” Porter foresees. The industry could take a lead in developing a widely accepted comprehensive LCA method that can be the basis for such legislation.
Share your stories on leisure marine industry with us
Do you have an innovation, research results or an other interesting topic you would like to share with the leisure marine equipment industry? The METSTRADE website and social media channels are a great platform to showcase your stories! Let us know via metstrade@rai.nl
Are you a METSTRADE exhibitor?
Make sure you add your latest press releases to your Company Profile in the Exhibitor Portal for free exposure.