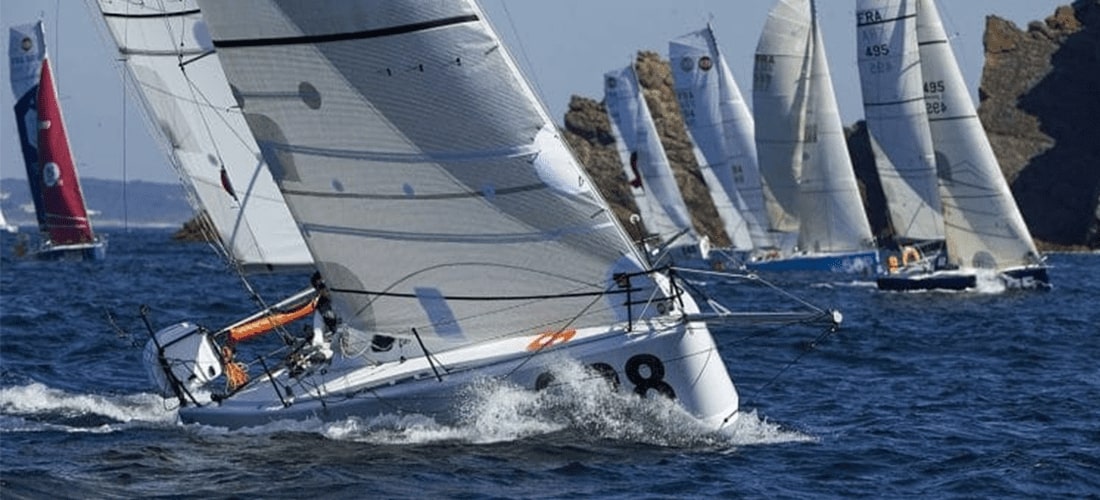
Some visitors to METSTRADE will be familiar with the name of Enrico Benco who started his company along with his partner Cristiana Talon, and the nice memorable name of ‘Go Sailing for a Change’ (GS4C) back in 2012.
Enrico has enthusiastically presented his ideas at previous sustainability forums during METSTRADE week. During this time, he has been developing a totally recyclable, ‘cradle to cradle’ model of the popular and well known Transat 650: a compact 6.5 metre ocean cruiser with a huge downwind sail area of 100m2 that has been competing in challenging single handed transatlantic races (known as the Mini-Transat, since 1977).
Enrico co-founded GS4C with a very clear mission in mind. With his partners in the company he has devoted the last six years to scouting innovative sustainable technologies and networking with companies in the composites business, in order to figure out all the necessary steps to achieve a ‘zero-landfill’ composite manufacturing process for boat construction. The plan is to participate in the 2019 Mini-Transat event with the first boat entirely made from sustainable fibre and recyclable bio-epoxy resin.
>
Global recognition at the JEC Awards
Over the last 15 years, the JEC Group, the largest composites organisation in the world, has involved 1,800 companies worldwide, and 177 companies have been rewarded for the excellence of their composite innovations via the JEC Innovation Programme.
GS4C’s Loop650 Sustainable Cradle to Cradle Sailing Boat, was nominated this year in the Sustainability Category, a well-deserved accolade for the several years work and practical application that Enrico and his team have dedicated to the project.
Enrico’s project was described in the details for JEC Award nominations as follows:
GS4C srl (Italy) and partners Entropy Resins (Spain), Isomatex (Belgium), Diab (Sweden), GIVIDI Fabrics (Italy), Cormatex (Italy.) For their sustainable, zero-landfill cradle-to-cradle industrial composite manufacturing technology demonstrator.
Key Benefits:
* Industrial ready
* Cradle-to-cradle recycling
* Zero-landfill manufacturing
* Low embodied energy
The Loop 650 project was devised as an example of industrial circular economy for the composite industry.
Presented at World Sailing’s Sustainability Conference.
In November last year the World Sailing Organisation gathered for their annual conference in Mexico, to set out their Sustainability 2030 aims and targets.
During this conference the forum delegates were shown a video of Enrico Benco being interviewed about the background, aims and achievements of GS4C and its strategic partners. Here is a transcript of some of the details given by Enrico to World Sailing about his venture.
Project based and collaborative
From the beginning, we set ourselves some tasks and then worked with a professional international network, our mission was to find the competencies and materials which enabled us to get those tasks accomplished. In the end, we settled on an enriched basalt fibre, and a bio based epoxy, which most importantly are both completely recyclable.
Full recycling without degradation
It’s also important to stress that the end-of-life recycled material from our project won’t be downgraded in any way, such as is often the case with resins and fibres that are chopped into smaller pieces, or recovered with a process which reduces their original integrity. What we have produced is a material that can go back into the manufacturing process as virgin material with the same properties as when it was used the first time around…a truly circular concept!
And, importantly both the fibre and the epoxy resin have very low embodied energy, meaning that they can be separated at the end-of-life using a low energy pyrolysis process.
Suatainable fibre derived from basalt
GS4C are using an enriched basalt fibre in their construction material matrix. Basalt is actually a lava from volcanic rock, which is melted, and then stretched into fibre in much the same way as glass fibre (used in GRP.) The real difference is that this material goes through a precise chemical analysis before being melted so that there is a known balance of all the constituent chemicals. So, because of this predictable chemical consistency it can go back into the furnace at end-of-life to be reconstituted to its original state.
Life cycle cost effective
Every material has a ‘life cost’ attached to it which has to be taken into account. Those materials that appear to be cheap are usually not recyclable, which means that somebody (or the environment) pays more for them eventually! The GS4C material will be competitive with a normal production GRP.
Production process consistency
Our original project scope was to make sure that the resulting material could be used with the usual competencies found in a boatyard. The fabric gets impregnated using infusion, meaning that it’s the same working process that is used in a GRP hull lay-up.
What next?
A lot has been learned since 2012, and GS4C intend to share their knowledge with others that can benefit from the use of the material they have developed. In fact, they are already talking with a high-volume sailing dinghy manufacturer.
And a foiling high performance Mini Transat is the next design in the pipeline. This will prove that the latest technology in high-end foiling yachts can be adapted to be built from fully sustainable materials.
Share your stories on leisure marine industry with us
Do you have an innovation, research results or an other interesting topic you would like to share with the leisure marine equipment industry? The METSTRADE website and social media channels are a great platform to showcase your stories! Let us know via metstrade@rai.nl
Are you a METSTRADE exhibitor?
Make sure you add your latest press releases to your Company Profile in the Exhibitor Portal for free exposure.